The Sigma Integrale DK2 motion system is a pure motion system for serious sim-racing enthusiasts, drivers and researchers. It is mechanically and electrically engineered around Sigma Integrale's unique motion algorithm to provide the most realistic and representative vehicle motion feedback with no pre-recorded canned effects.
Processing time for new orders is 3-5 days.
Why Sigma Integrale?
Sigma Integrale's unique approach to motion systems made them a globally recognized name among sim racers and North America's leading manufacturer of motion systems. Made entirely out of billet aluminum, Sigma Integrale linear actuators's strength and durability are without equal. Entirely engineered, tested, and built in the US by Sigma and operate using Sigma's own algorithm that prioritize realistic motion, they pioneered full-vehicle simulators using actual production cars from manufacturers including Chevrolet, Dodge, Peterbilt, VW, and others.

Backed by real-world racing, coaching, and HPDE experience, we at Pit Lane Sim Racing have always been big advocates of motion simulation but not all motion systems are created equal. This is why we carefully choose motion systems, which allowed us to be one of the very few with real experience building motion simulators in every configuration including 2 DOF, 3 DOF, 4 DOF, 5 DOF, and 6 DOF.
Key Features
- Completely made from billet aluminum for optimal haptic transfer
- 2-inch (50mm) solid steel piston for exceptional side loading
-
American made Teknic motors and controllers for exceptional signal control
- Advanced motion algorithms controlling speed, acceleration and jerk in real-time
- True Haptic algorithm simulating high frequency vibrations with no canned effects.
- Years of maintenance free operation with no lubrication required
- Silent operation
High Dynamic Mass Actuator Design
All DK motion systems are made in the USA from a solid piece aluminum for optimal strength, durability and the best haptic feedback translation. Machining from billet aluminum is significantly stronger over other methods of production such as casting, bolted assemblies or 3D printing. Each system also features a solid 2” OD steel piston and oversized ball screws for optimal smooth performance and long service life with no maintenance required. The DK system installs in less than 30 minutes to almost any aluminum extrusion with our own billet aluminum brackets and components.
Motion Specific Electrical System
Sigma uses premium American-made Teknic integrated motors specifically tuned to run Sigma’s advanced motion algorithms. At double the price of conventional motors, the servos have three times the performance of conventional motors. We are also the only company to feature 75VDC electrical architecture for various performance standards. Each motor is optically isolated guaranteeing zero electrical or magnetic interference. Cable lengths from the controller to the motors can go up to 150-feet and the controller connects via an ethernet cable to the computer for optimal signal integrity. The controller is switchable between 120/240v and ships with power cables and accessories specific to your region.
Specialized Motion Software
Sigma takes a first principles approach with our motion software and algorithms. We design, build and develop all our embedded and motion software in-house. This allows us to achieve absolute control of our simulation specific control of its mechanical and electrical integration. Our software features specialized motion layers and unique algorithms to achieve what we call Motion Integrity or the most accurate representation of simulated motion. Pitch, roll, heave, environment, and our True Haptic engine and road vibrations are some of the best in the industry. Our software also installs quickly and has automatic over-the-air software and firmware updates. Remote tuning and control of the system is convenient and can be done in real-time with a secondary device without having to stop and exit simulation software.
No Motion Effects or Gimmicks
DK2 takes a modern approach to our signal processing and motion control to create the most responsive system on the market. Every elevation change, vehicle movement, surface change and gear shift, is captured and reproduced within 2” (50mm) of the available mechanical stroke. The same first principles approach is applied to high frequency vibrations with no canned effects. Focusing on pure signal processing, it results in less tunning and more driving.
Specifications
- Max payload: 500 lb./227 kg (4 actuator system)
- 375 lb/170 kg (3 actuator system)
- Max displacement: 2.0 in./50.8 mm
- Max speed: 213 mm/s
- Weight: 10 lb. (per actuator)
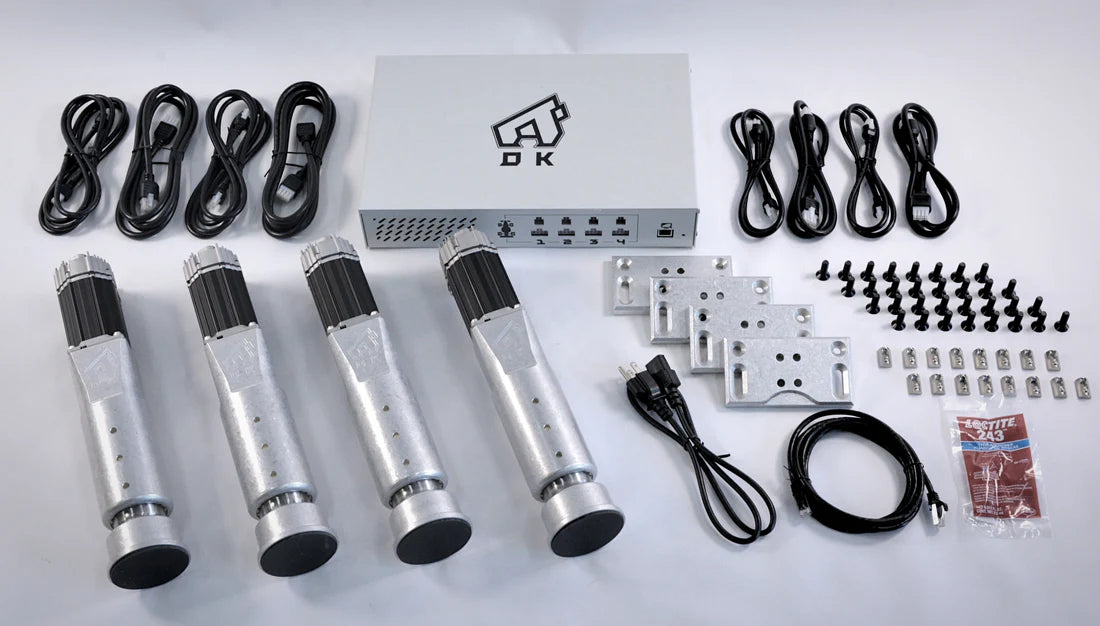

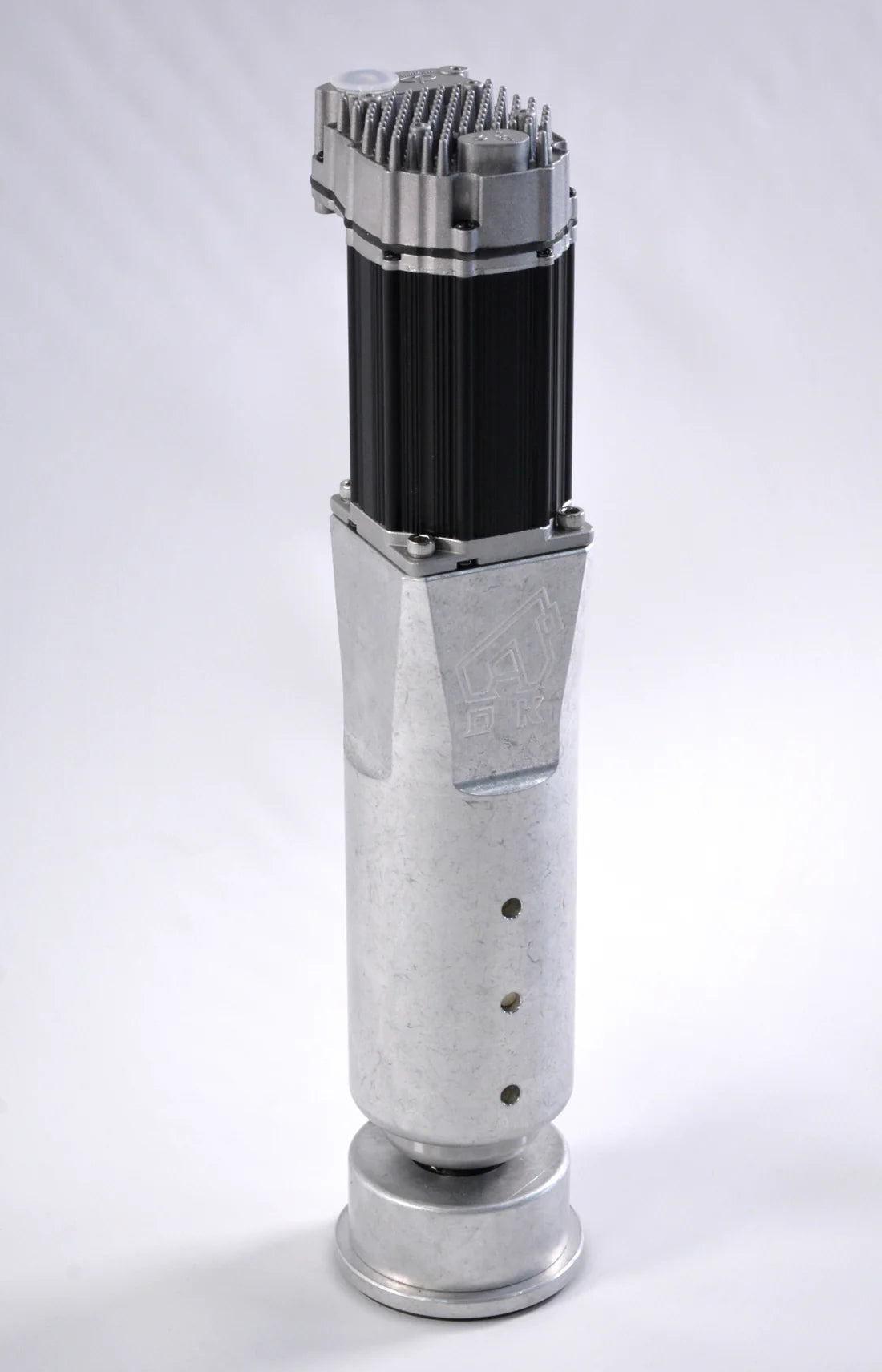
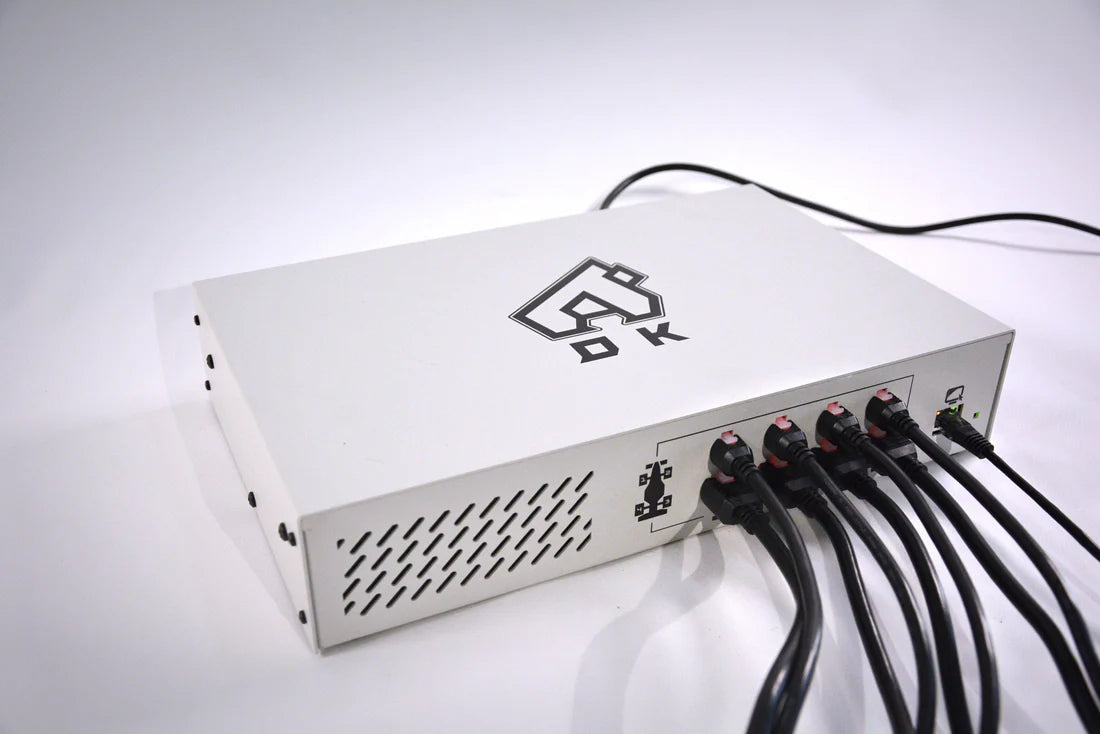
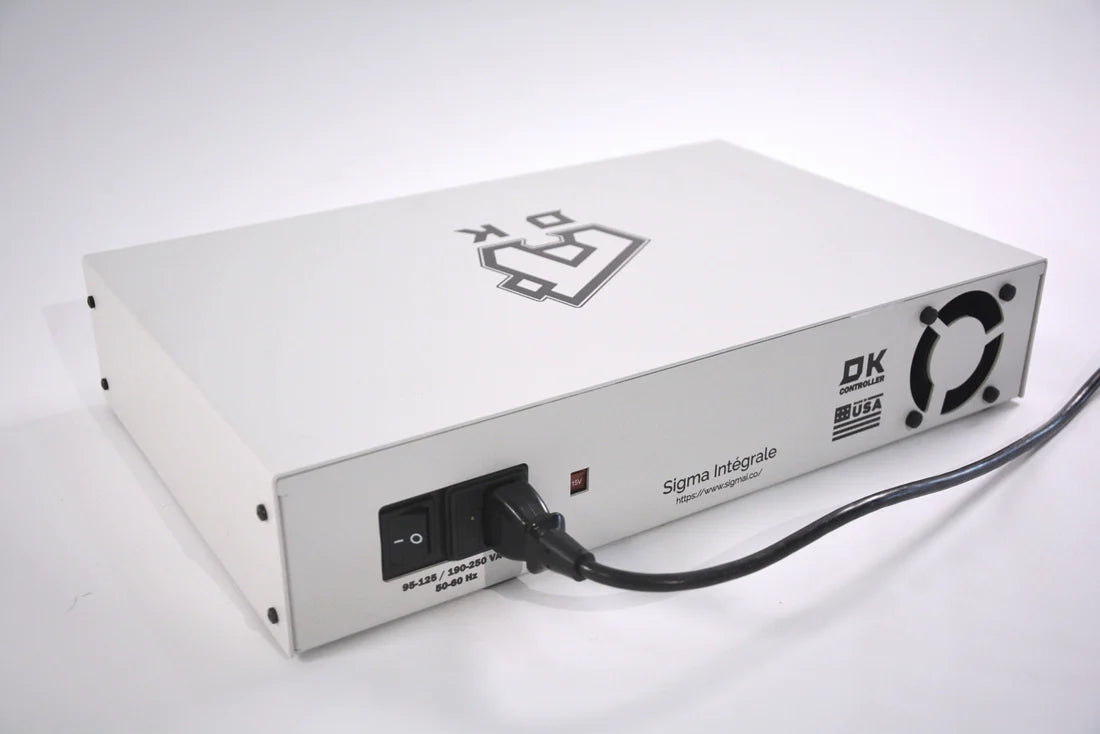